For more than 100 years, Jack London’s adventure novel The Call of the Wild has been celebrated as a powerful testament to the beauty of nature. When 20th Century Studios set out to adapt the book as a film in 2018, the studio sought to honor this legacy by producing the film in the most environmentally responsible way possible. From the earliest days of production, the cast and crew dedicated themselves to reducing waste, recycling used materials, prioritizing responsible food service, and embracing renewable energy. These efforts helped the project divert more than 82% of its waste from landfill and generate significant cost and carbon savings in the process.
The Call of the Wild follows John Thornton, played by Harrison Ford, as he treks across the Yukon Territory during the Klondike Gold Rush of the 1890s, a story of ambitious scope that posed a number of sustainability challenges. To accurately bring the story to life, the Construction Department would have to erect multiple era-appropriate Alaskan towns, the Special Effects Department would have to create tons of fake snow, and the extensive use of outdoor locations would make it much more difficult to access clean energy sources. However, the leadership team of Executive Producer Diana Pokorny, Production Supervisor Gavin Behrman, and Sustainability Manager Adrienne Pfeiffer worked with the crew to meet every obstacle as it arose.
Pfeiffer met with each department before filming began to set environmental goals for production, develop the best strategies to meet these goals, and track progress throughout the nearly six-month shoot schedule. As these conversations took place, crew members across the production began to make suggestions for greater sustainability, including Stunt Coordinator Charlie Croughwell, who in 2015 founded a nonprofit called the Earth’s Oceans Foundation. The organization recycles and repurposes used plastics into new products for commercial and personal use, such as building materials, exercise equipment, boating safety gear, and more. The Call of the Wild began working with Earth’s Oceans Foundation just a few weeks after filming began, and over the course of the production, the organization recovered 4.75 tons of used plastics from the set, including hard-to-recycle plastics such as latex gloves, latex sponges, and dirty foam.
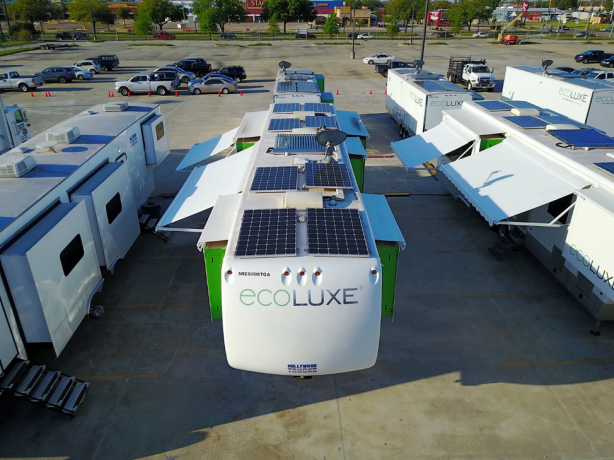
The Call of the Wild’s sustainability efforts spanned across every department and filming location, with food service, set construction, and renewable energy emerging as the major focus areas. Some of the highlights from the production included:
- Single-use plastic water bottles were banned at each of the film’s six filming locations in favor of refillable ones, which were gifted to the cast and crew. This practice avoided the use of more than 200,000 plastic bottles, saving more than $33,000.
- Craft Services committed to a rigorous food service plan, consistently offering vegan dining options, selecting local, organic food products, and providing biodegradable, compostable plates and cutlery. More than 30,000 pounds of food and cutlery were composted, avoiding the emission of 22,111 pounds of greenhouse gases (CO2e).
- Leftover food was collected and donated to those in need in the California communities where the movie filmed, through partnerships with the Hollywood Food Coalition and Rock and Wrap It Up. The crew collectively donated 1,515 pounds of food, providing more than 1,250 meals.
- The movie filmed for more than a month at Sable Ranch in Santa Clarita, California, which allowed the crew to install long-term solar-powered generators, electric vehicle charging stations for crew use, and solar-powered trailers.
- The crew purchased two solar-powered work lights for use at the Sable Ranch base camp, then quickly expanded their stock to eight once the lights’ high quality and energy efficiency was discovered firsthand.
- Sable Ranch asked for theThe Call of the Wild sets to remain on their land permanently, for use in future film projects. This reuse of materials avoided tons of landfill waste.
- Vendor DeRouchey Foam bought back 17 of the 21 tons of foam purchased by the Set Construction for reuse and recycling.
- The production office purchased 100% recycled content paper for white copy paper and 30% recycled content paper for colored copy paper. This policy saved more than 1,044 pounds of greenhouse gas emissions.